
Originating in the early 1970s, JIT emerged as a management philosophy in Japan. Taiichi Ohno pioneered and refined it at Toyota manufacturing plants and is widely regarded as the founding figure of the Toyota Production System.
While Ford is credited with inspiring Ohno's JIT system, both Ford and Toyota were already embracing the concept. During a U.S. visit, Toyota was impressed by Piggly Wiggly's efficient inventory management, where products were restocked based on customer demand, maintaining a balance between supply and demand.
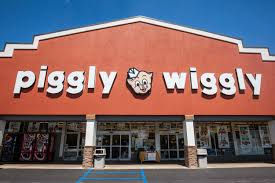
Just-in-time manufacturing, or JIT, is a management approach focused on producing and delivering goods to meet customer demand precisely when, where, and in the required quantities. Instead of stockpiling items based on assumptions, JIT involves supplying only what is requested by the customer.
JIT aims to reduce the 7 Wastes of Lean: waiting, overproduction, and excessive inventory, in contrast to the common JIC production approach.
Can JIT be applied to both manufacturing and non-manufacturing contexts?
Indeed, the representatives from Toyota in Japan were impressed by the efficient shelf inventory management of a small chain of Piggly Wiggly convenience stores, not by Ford. Having extensive stocks of raw materials and finished products may not always be beneficial. In many instances, the necessity for large inventories is unnecessary. Streamlining the supply chain and minimizing inventories can lead to significant cost savings for most organizations.
Comments