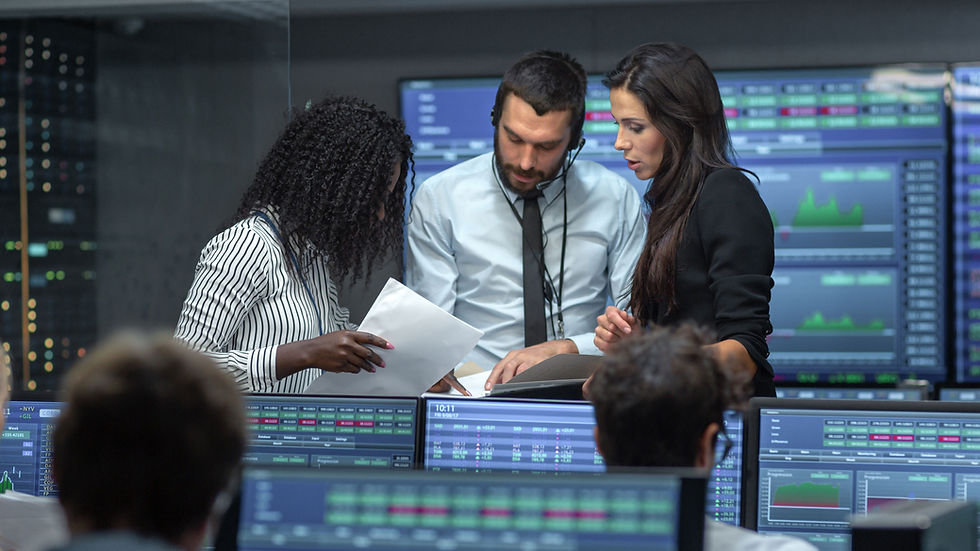
Statistical Process Control (SPC) is a compelling collection of tools that enables you to observe your process, pinpoint sources of variation, and offer guidance on enhancing it.
Let's delve into the details of each one, the advantages of SPC, and how you can utilize these tools to understand better the insights provided by your process data.
Overview: What is SPC?
Change is constant. The time it takes for you to drive to work changes daily. Your weight fluctuates every time you step on the scale. The data you collect varies each time you measure something. Variability is a natural result of any process. SPC can assist you in comprehending variability and advise you on how to respond.
The control chart, a key tool of Statistical Process Control (SPC), was created by Dr. Walter A. Shewhart in the 1920s. During World War II, SPC was widely employed to boost material output for U.S. war endeavours. Dr. W. Edwards Deming travelled to Japan following the war and introduced SPC to Japanese engineers and business executives.
Shewhart noticed that operators often adjusted the machines on the production line, leading to increased variability in output. His aim was to create a straightforward device that could indicate to the operator when adjustments were necessary and when they were best to keep the machine unchanged.
Shewhart introduced the control chart to detect random variation, known as common cause variation, and special cause variation, which arises from specific, identifiable causes. He utilized this statistical method to oversee and regulate the process.
When using the SPC technique, process data is graphed chronologically. Based on the data, control limits are determined to identify expected or common cause variation. If data points exceed these limits or show non-random patterns, it indicates the possible presence of special cause variation. Examining the factors related to such data points is advisable to determine the underlying cause. If the process shows enhancement after a change, incorporate it for ongoing improvement. Otherwise, strive to eliminate the reason behind the alteration.

3 advantages of Statistical Process Control:
Distinguish between common and special cause variation:
The control's objective is to differentiate common variation from special variation. By recognizing this distinction, you can determine whether intervention is necessary.
Quick Feedback :
After plotting your data on the control chart, you can determine whether the variation is due to common reasons or special causes. This immediate feedback allows for prompt action.
Decreased variation in the process:
To minimize unnecessary process adjustments, focus exclusively on addressing and acting upon special-cause variation. Continuous interference with the process and excessive adjustments only amplify process variation.
Why is it important to understand SPC?
Nowadays, statistical software handles most of the control charting tasks, making a deep knowledge of statistics unnecessary. The key is to understand how to interpret the control chart and know the appropriate actions.
Knowing when to act and when to refrain from acting:
Depend on the control chart signals to determine when to investigate special cause variation. When dealing with common cause variation, focus on enhancing the process rather than trying to justify a single data point.
Statistical Process Control (SPC) applies to any process:
Control charts are suitable for all kinds of data, whether continuous or discrete, as long as it is gathered sequentially over time.
Informs you about the timing, not the reason:
SPC informs you about the occurrence and timing of events but does not provide insight into their reasons. When a special cause signal is present, an investigation into the process is necessary to determine the likely cause.
Commentaires